開頭:
在塑料擠出成型過程中,溫度控制是決定產(chǎn)品質(zhì)量的核心因素之一。過高的溫度可能導(dǎo)致材料分解,而過低的溫度則會引起塑化不均、表面粗糙等問題。無論是新手操作員還是經(jīng)驗豐富的工程師,都需要一份精準的擠出機塑料溫度參考表作為工藝調(diào)整的依據(jù)。本文將從材料特性、溫度區(qū)間設(shè)定及常見問題三個維度,為您解析如何科學(xué)控制擠出溫度。
一、塑料材料與溫度的關(guān)系:從熔點到分解點
每種塑料的加工溫度窗口由其熱穩(wěn)定性和熔融特性決定。例如,聚乙烯(PE)的加工溫度通常為180-240℃,而聚碳酸酯(PC)需要更高的280-320℃。以下是常見塑料的溫度范圍參考表:
塑料類型 |
料筒溫度(℃) |
模具溫度(℃) |
LDPE |
160-220 |
30-60 |
HDPE |
180-240 |
40-70 |
PP |
200-260 |
40-80 |
ABS |
210-250 |
50-80 |
PVC(硬質(zhì)) |
170-190 |
30-50 |
PET |
260-290 |
80-120 |
注:以上數(shù)據(jù)為通用參考值,實際需根據(jù)原料牌號、添加劑類型及設(shè)備性能調(diào)整。
二、擠出機溫度分區(qū)的科學(xué)設(shè)定
現(xiàn)代擠出機的料筒通常分為3-5個加熱區(qū),每個區(qū)域的溫度需梯度遞增,以實現(xiàn)材料的逐步塑化。以PP加工為例:
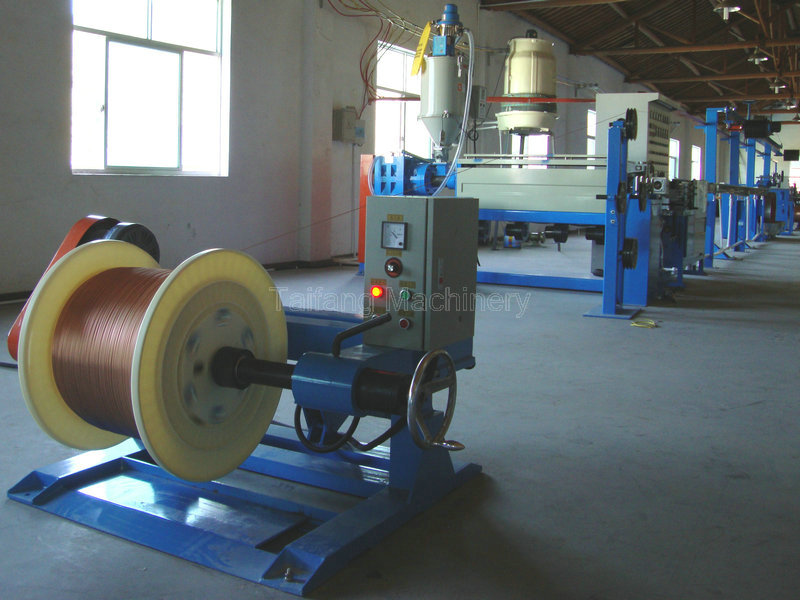
進料段(第1區(qū)):180-200℃——初步軟化顆粒,避免過早熔化導(dǎo)致喂料堵塞;
壓縮段(第3區(qū)):210-230℃——通過剪切熱促進塑化均勻性;
計量段(末區(qū)):240-260℃——確保熔體流動性,減少擠出壓力波動。
關(guān)鍵提示:模具溫度對產(chǎn)品尺寸穩(wěn)定性影響顯著。例如,PET瓶坯成型時,若模具溫度低于80℃,可能導(dǎo)致結(jié)晶度不足,產(chǎn)品易變形。
三、溫度異常引發(fā)的典型問題與解決方案
焦料或黃變
- 成因:料筒末端溫度過高,或物料停留時間過長;
- 對策:降低最后兩區(qū)溫度5-10℃,檢查螺桿磨損情況。
- 表面波紋或鯊魚皮現(xiàn)象
- 成因:熔體溫度過低,流動性不足;
- 對策:提升計量段溫度,增加螺桿轉(zhuǎn)速(需平衡背壓)。
- 氣泡或銀紋
成因:原料含水率超標,或分解氣體未充分排出;
-
對策:在進料段增設(shè)抽真空裝置,預(yù)熱溫度提高至80℃以上。
四、進階技巧:溫度與其他工藝參數(shù)的協(xié)同優(yōu)化
- 螺桿轉(zhuǎn)速與溫度的動態(tài)平衡
提高轉(zhuǎn)速時,剪切熱會增加熔體溫度。此時需降低加熱功率,避免局部過熱。
- 添加劑對溫度的敏感度
- 填充玻璃纖維的PA6:需降低溫度10-15℃,防止纖維降解;
- 添加阻燃劑的ABS:加工溫度上限減少20℃,以保持阻燃效率。
紅外測溫與閉環(huán)控制
采用非接觸式紅外傳感器實時監(jiān)測熔體溫度,可減少人工干預(yù)偏差,提升良品率3%-5%。
五、特殊材料的溫度管理要點
生物降解塑料(PLA)
- 加工窗口窄(170-190℃),需精確控制溫度波動在±3℃以內(nèi);
- 模具冷卻時間延長至普通PE的1.5倍,防止收縮翹曲。
- 高溫工程塑料(PEEK)
- 料筒溫度需達到350-400℃,需選用特種合金螺桿;
- 停機前必須用HDPE清洗料筒,避免碳化殘留。
通過上述分析可見,擠出機溫度設(shè)置并非一成不變,而需結(jié)合材料特性、設(shè)備狀態(tài)及產(chǎn)品要求靈活調(diào)整。建議企業(yè)建立專屬的工藝數(shù)據(jù)庫,每次換料時優(yōu)先匹配歷史成功參數(shù),再逐步微調(diào)優(yōu)化。
TAG: